Awesome Earthmovers Magazine Interview
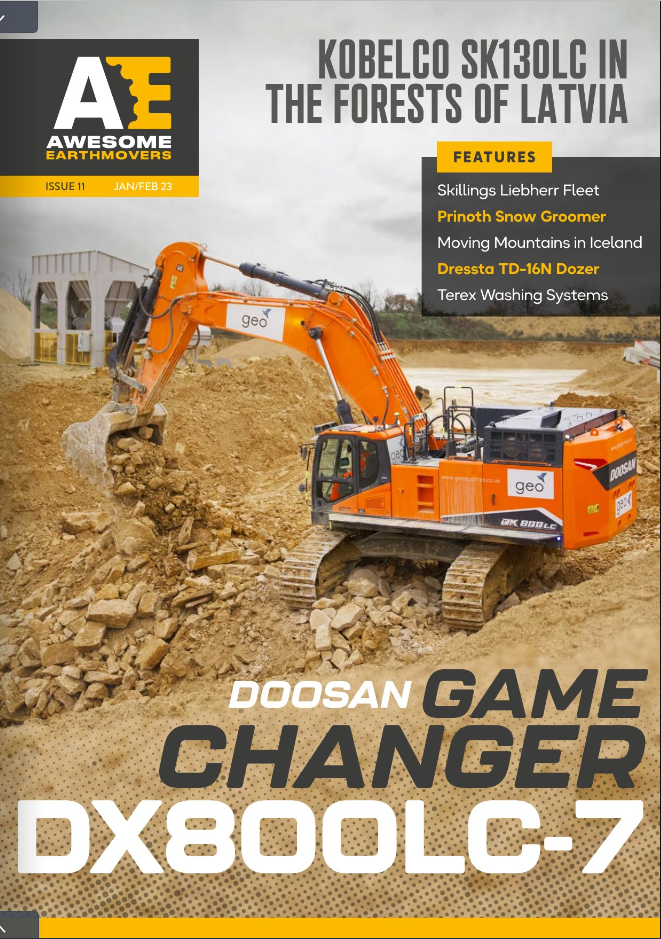
Dan Smith, our Technology Products Manager speaks with the latest edition of Awesome Earthmovers magazine. Read the article below and find the full magazine here: Awesome Earthmovers Issue 11
(For the full podcast interview see here.)
Moving into the Digital Age
Specialising in helping contractors transition from traditional engineering methods and giving them the tools and knowledge to drive their business forward into the digital age, Machine Control & GNSS rental supplier, retailer and site services provider MDiG, since its launch in 2020, has been building an extensive customer base across the UK from its Redditch based headquarters.
It is doing so against a backdrop of a digital revolution in the construction industry which, says Highways England, could dramatically increase productivity and save billions of pounds, while radically reducing disruption to the public and slashing the number of fatal building site accidents.
The organisation is spearheading a 15-year plan to accelerate the use of technology in infrastructure and says the CAP (Connected and Autonomous Plant) roadmap, developed through collaboration with more than 100 industry stakeholders, could see annual savings of £53 billion across new construction work, in addition to improving productivity by up to £400 billion by 2040.
Getting to that point, however, will be a challenge for many in the industry, which is where MDiG aims to make a difference. MDiG’s Technology Products Manager Dan Smith says adopting new technology on the jobsite can be a daunting task for some, and costly, too.
“There’s no doubt, technology can be a big investment and we understand that, which is why we offer rental options to make digital construction available to everyone,” he says. “As dealers for Leica and Topcon machine control systems, Smart Construction and Xwatch site safety and protection solutions, we believe our construction technology will help contractors achieve goals they simply cannot reach manually. With the correct technology in place, it’s possible to project business into a new era of construction.”
As one of the founding members of MDiG, Dan comes from a civil engineering background and has worked as a site engineer, with more than 15 years experience with machine control. From small beginnings, MDiG now boasts an 18-strong team that includes two Account Managers driving business forward, installers and trainers who have a combined knowledge of 50 years in machine control. With business continuing to grow and expand, the company has increased its rental fleet of Topcon and Leica products accordingly to meet that demand from the industry.
“While some are already well on the road to connected and autonomous plant, others have yet to dip their toes, as it were, into the world of GPS and machine control, put off by what could be a massive outlay for them; renting is by far the easiest route to ease themselves into that environment, especially if they operate machines that are plug and play ready, as most already are today.”
“When you weight up the rental costs against the on-site benefits, it makes sense to employ machine control and site safety solutions”
Of course, before any machine control project starts the appropriate GNSS base equipment must be sourced and then precisely set-up. Mistakes are easy to make, hard to detect, and can compromise efficiencies throughout the entire project.
“Choosing the right equipment for a digital job site is essential,” says Dan. “Our team of specialists advises customers on which kit to choose – from Base Stations and GPS Rovers to Machine Control Kits and Total Stations – and provide installation and ongoing support from start to finish. When you weight up the rental costs against the on-site benefits, it is not difficult to see that it makes sense to employ machine control and site safety solutions.”
As we mentioned, though, adopting digital technology can be challenging and difficult for some. “We understand and appreciate that, which is why we have developed a suite of training courses on all of the products we rent and install,” comments Dan. “We show them how machine control works, how they can get the best out of job sites and how it can increase efficiency and productivity. These bespoke courses are ideal for those who are new to digital construction and machine control and for those simply looking to brush up on their knowledge.”
There are course on Leica and Topcon machine control systems for site engineers, taking them through everything they need to know when it comes to job site setup, data synchronisation, troubleshooting and the daily use of machine control. The training involves classroom-based training and site exercises to maximise learning.
Other courses for dozer and excavator operators will take them through the hardware components and the benefits of machine control, followed by an indepth look at the main run screen components and all the tools on board to help in day-to-day tasks and to get the most from the system. From logging survey points to creating bespoke surfaces for the jobsite, these courses will make sure operators are fully up to speed.
Employing cutting edge aerial equipment, its CAA Pilots can save time and money on any project
Another growing side of the MDiG business is in the use of drones which are increasingly popular on jobsites. Currently, they have four fully trained drone operators on the team offering a range of services. Aerial insights improve progress tracking and help catch problems early before they become costly or add weeks to a project’s timeline.
Employing cutting edge aerial equipment, coupled with up to date processing software, its CAA Pilots can save time and money on any project. With multiple deliverables, they can deliver quick volumetric reports to aid in any part of the construction process, with the ability of patching into any original workflow, utilising industry standard file formats. Packages range from quick stockpile volume calculations to expansive cut/fill reports.
Clearly, the construction industry is ever-evolving. Looking forward, no site, big or small, will be complete without the latest digital technology. “We want to help our customers to get ahead of the curve and believe our products are essential for future success. Our products will enable all to embrace the change.“
To see which products would suit your project, jobsite and budget please contact one of our Account Managers:
South – Katie Clarke, 07831 499209, katie.clarke@mdig.co.uk
North – Simon Ralph, 07918 287318, simon.ralph@mdig.co.uk